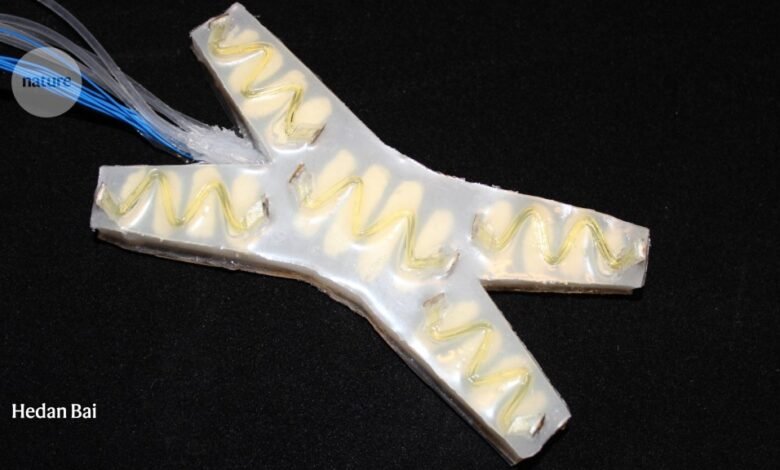
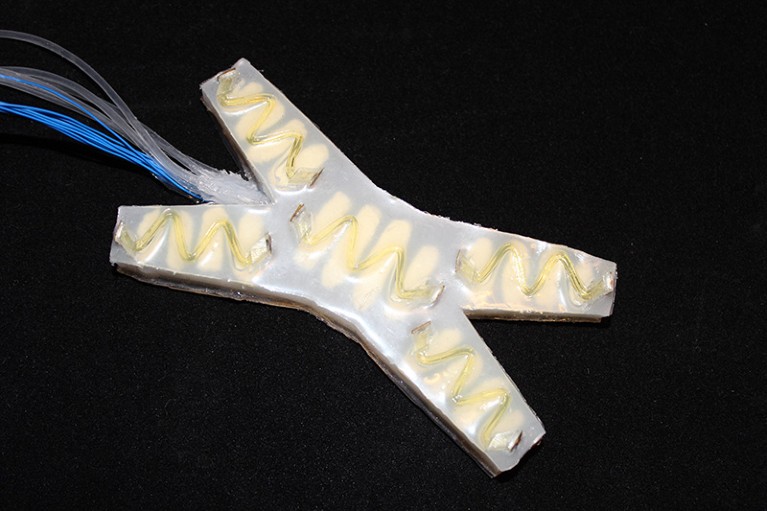
This soft-bodied robot knows when it has been damaged and can heal itself.Credit: Hedan Bai
Inspiration can come from just about anywhere. For Robert Shepherd, a roboticist at Cornell University in Ithaca, New York, the source was a football injury 20 years ago, when he tore his anterior cruciate ligament. He needed surgery to re-attach the ligament to bone, but his skin and nerves healed by themselves — something that the tactile-sensing robots he was building at the time could not do. “If these sensor networks get damaged, that’s it,” Shepherd says. In the years since, he and his team have worked to correct this by designing robots that can detect and repair the damage that they sustain. In 2022, Shepherd’s group demonstrated a robot that could recognize damage inflicted by multiple stabbings, stop what it was doing and heal itself1. It would then start off in a different direction in an attempt to avoid further injury.
Part of Nature Outlook: Robotics and artificial intelligence
For robots that operate in dangerous or remote locations, such as space or the deep sea, the ability to make repairs without human intervention would be invaluable. And if robots become commonplace in human society, self-healing could greatly reduce the quantity of electronic waste that would otherwise be sent to landfill.
Researchers have developed numerous techniques and materials that could make possible a variety of self-healing electronic components and structural parts. What remains is to integrate these diverse demonstration technologies into sophisticated, damage-resilient machines. “A lot of effort has been focused on different strategies for self-healing,” says Benjamin Tee, an engineer at the National University of Singapore. “The next step is to evolve to systems.” Eventually, this work could perhaps yield machines with not only the resilience to withstand injury, but also the intelligence to see it coming.
Material advances
Most research on self-healing uses polymers — large molecules made up of repeating parts. Many synthetic polymers are formed by cross-linking long polymer chains together into networks using strong covalent bonds. A commonly used self-healing technique exploits a process called the Diels–Alder (DA) reaction. If a damaged polymer is heated, the remaining covalent bonds holding the chains together will break. But when the material cools, the DA reaction forms new bonds. The result is polymers that heal when they are heated and then cooled. Clever chemistry has also produced materials that use other triggers instead of heating, including pH, pressure and specific wavelengths of light.
Healing that requires a trigger is called non-autonomous healing. By contrast, some other materials demonstrate autonomous healing, knitting themselves back together when damaged without the need for any stimulus. Mechanical engineer Bram Vanderborght and his colleagues at Vrije University Brussels have developed DA-based polymers that can autonomously heal at room temperature2. The key to this was altering the cross-link density, which changes molecular mobility, and in turn the tendency for molecules to find and bond with others.
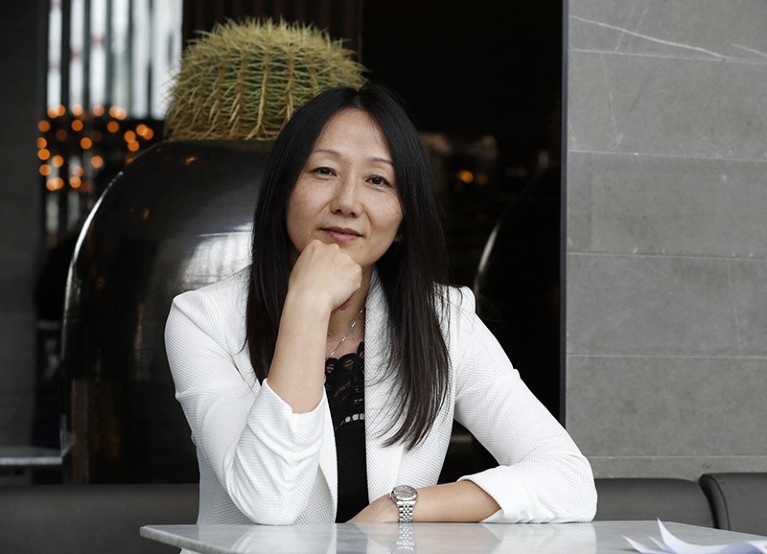
Chemical engineer Zhenan Bao and her team have developed electronic skin that can self heal.Credit: FRANCOIS GUILLOT/AFP via Getty
Another approach to creating polymers that are capable of autonomous self-healing uses hydrogen bonds. These are formed by the attraction of positively charged hydrogen ions to negatively charged atoms in a molecule and are weaker than covalent bonds. “Because the bonds aren’t strong, they’re not permanent, so these polymer networks are continuously forming and dissociating,” says Zhenan Bao, a chemical engineer at Stanford University in California. “When we cut the material the bonds break, but when you put two pieces together, hydrogen bonds form very readily and the material recovers.” Weak bonds also make materials stretchy. Combining multiple kinds of bond, of different strengths, produces materials that are both strong and flexible.
For robots, materials capable of autonomous healing will usually be preferable. However, there are circumstances in which it could be useful for a robot to wait for the right time to repair itself. “Maybe it’s doing work it cannot stop,” Vanderborght says, or the humidity in the environment is not suitable for healing. “A robotic system is more than the material, it also has intelligence,” Vanderborght says. “With non-autonomous healing, we can choose the optimal moment to heal.”
Electrical signals
Polymers are excellent materials to make soft, pliable grippers, but they are typically not much use for electronic components, because most do not conduct electricity. To make a robot with self-healing electronics, researchers first need conductive self-healing materials. One approach involves adding conductive fillers, such as carbon nanotubes, metal particles or nanowires, to self-healing polymers. Bao used these techniques alongside then-graduate-student Tee to develop self-healing electronic skin that contains strain, pressure and other sensors3. The material is capable of tactile sensing, and its softness could make it safer to operate around people than more conventional hard-bodied robots.
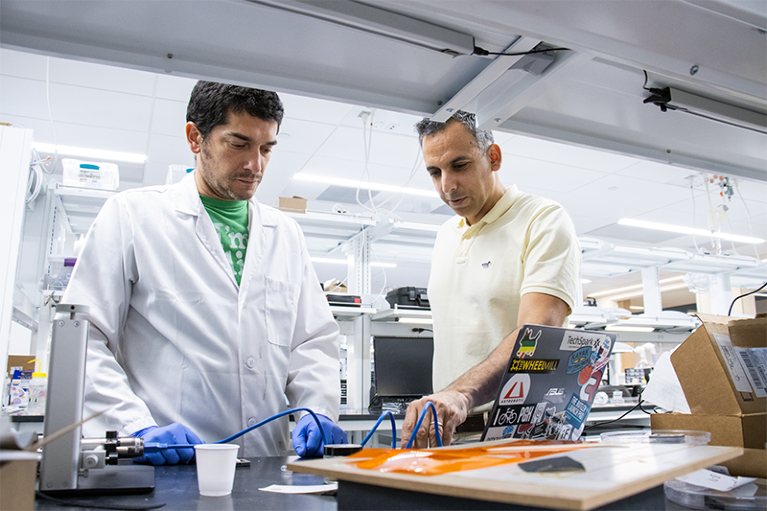
Mechanical engineer Carmel Majidi (right) and his team came up with a conductive and pliable self-healing gel.Credit: Soft Machines Lab, Carnegie Mellon University
Another way to make self-healing polymers conductive is by adding liquid metal. Mechanical engineer Carmel Majidi at Carnegie Mellon University in Pittsburgh, Pennsylvania, and his colleagues suspended droplets of a liquid metal alloy made up of gallium and indium in an elastic polymer to create autonomously self-healing soft electronics4.
Polymer–liquid mixtures called ionic gels, that conduct using ions rather than electrons, have also been proposed for self-healing electronics. Their capacity to conduct electricity, however, is typically limited. “Conductivity is good enough for basic sensing, but you can’t really use it to transmit signals,” Majidi says.
To address this, Majidi and his colleagues took an ionic gel containing silver flakes and added their liquid metal alloy. The result was a highly conductive and extremely pliable self-healing gel. When the gel is damaged, hydrogen bonds knit it back together and the liquid metal quickly restores conductivity. In 2023, Majidi’s team reported using the material to power the motor of a robot snail5. “The idea is to create robots that have the same properties natural nervous tissue has: an ability to collect and transport signals,” Majidi says.
Researchers have also developed self-healing polymers with more complex electronic properties — dielectrics and semiconductors, for example. These are useful for making components such as capacitors and transistors that can repair themselves. Tee and his colleagues have developed a transparent self-healing dielectric, which they used to construct low-power light-emitting capacitors. In 2019, the team demonstrated the technology in a soft robotic gripper that can detect objects in the dark by reflecting light off them6. The material can also heal in water owing to the hydrophobic ion–dipole bonds that hold it together, and it can work at a variety of temperatures and pHs7. “This is the second generation of self-healing autonomous materials,” Tee says.
As electronic components increase in complexity, they tend to use multiple layers. This presents a problem for healing: when such components are repaired, the layers can require painstaking manual realignment that is often not possible for very thin devices. Last June, Bao and her colleagues proposed a solution to this that involves stacking alternating layers of two polymers8. The polymers do not mix, ensuring that the layers remain distinct, but they can adhere into a single material by forming hydrogen bonds where they meet. When this multilayer material is cut and then heated, the affinity the different polymers have for themselves — and their aversion to each other — causes the layers to realign. The researchers have demonstrated the approach in a self-healing pressure sensor, and in a robot in which the large components were first roughly magnetically assembled, and then microscopically aligned by heating.
Sensing pain
To respond to injury, an intelligent machine must first notice when it happens. In humans, pain provides the alert. For robots, sensors made from conductive polymers can use changes in conductance to detect damage. Vanderborght’s group used a DA polymer that contained conductive carbon particles to create piezoresistive strain sensors, which detect force by sensing a change in electrical resistance, and capacitive touch sensors9. The team then embedded these sensors in a soft polymer robot gripper, enabling it to detect deformation and force. These sensors also inherently detect severe damage because cuts and tears cause sudden changes in resistance or capacitance.
This information could then be used to initiate healing. Vanderborght’s group has developed a self-healing resistive heater that can be integrated into a soft robot10. When the robot detects a change in resistance or capacitance that is consistent with an injury, it could then switch on this heater to begin the healing process.
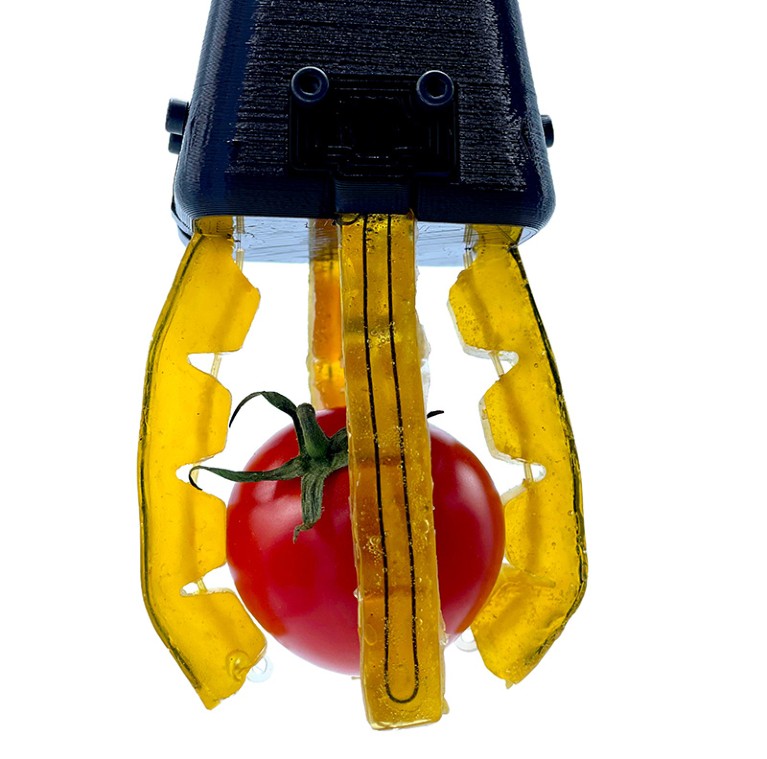
A strain sensor embedded into a robot gripper can detect injury.Credit: Ref 9
Conductive sensors have some drawbacks: they are both electrically noisy and complicated to make, says Shepherd. For this reason, he and his team are exploring the possibility of using light to detect damage. The team has shaped a self-healing polyurethane-based material that transmits light into optical fibres1. Stretching or bending the fibres alters the amount of light transmitted, allowing a processor to detect deformation and damage.
The material incorporates two kinds of bond: covalent disulfide bonds and weaker hydrogen bonds. “It uses hydrogen bonding, so it immediately heals,” says Shepherd. “But it also uses disulfide exchange over a longer period, to make it strong.” The researchers incorporated the optical fibres into a soft quadruped robot that stops walking while it heals. “Then, after a long enough period, it starts moving again,” Shepherd says.
Whichever technology is used to detect an injury, the same metrics could also be used after healing to evaluate the extent of recovery. Shepherd’s group is using neural networks to analyse the outputs of optical-sensor networks, to recognize different states of deformation and damage. In the future, Shepherd plans to use this to enable a self-healing robot to compensate for any deficits that remain after repair. “You can update the controller to say, ‘even though it’s repaired, we’ll now sense differently in this region’, then operate based on that change,” he says. Shepherd compares this to his own injury. It is “what happened to my knee — the nerves healed on their own, and they feel very different than before, but I can still use that sensation to interpret the world”.
Blood and bone
A crucial component of any robot is its power source — if that fails, everything does. Self-healing batteries have been developed, and there are devices that harvest energy from movement, light or temperature, but their output tends to be low. Shepherd and his colleagues are pursuing a radically different solution.
Based on flow batteries, which store power in electrolytes, the approach uses an electrolyte for the fluid in hydraulic robots. The team was inspired by natural vascular systems that carry oxygen and nutrients throughout the body, remove waste and fight infections. In a soft aquatic robot, the synthetic vascular system operated the robot’s fins and powered its pumps and electronics11. And in a different set-up, vibrating ions in the electrolyte meant the system could even be used to transmit information12. “These liquid wires are a self-healing system we’re imbibing into robots, which we call robot blood,” Shepherd says. “Liquids are the ultimate self-healing material, if you can contain them.”
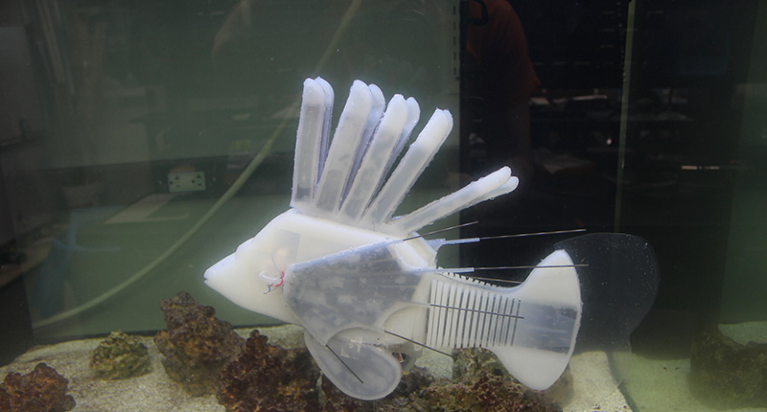
A synthetic vascular system works the fins of a lionfish-inspired robot.Credit: James Pikul
James Pikul, a mechanical engineer at the University of Pennsylvania, Philadelphia, who worked with Shepherd on these electrolytic vascular systems, is now focusing on ways of using liquid systems to heal metal components13. “We were very inspired by the way bone is repaired,” says Pikul. “Your body pumps blood to the fracture, which delivers nutrients, energy and the building blocks you need to restore the bone.”
Metals are stronger than the polymers most researchers in this field have focused on, which could be an advantage for robots intended for heavy-duty industrial applications. “There’s a trade-off for self-healing materials: if they heal fast, they’re usually soft and not mechanically strong,” says Bao. Metals are, of course, eminently repairable by heating above their melting temperature, but the energy needed to do this is prohibitive in a robot. The extreme temperatures would also not be ideal for a machine containing delicate components.
Instead, Pikul’s metal-healing technique exploits oxidation–reduction (redox) reactions. Taking electrons from metal atoms (oxidation) turns them into positive ions, which can be moved using electric fields. Giving electrons back (reduction) returns the ions to neutral metal atoms, which are deposited in the new location. This is a well-established process and is the basis of electroplating. “By doing this, we can move metal from one place to another,” Pikul says. “All we have to do is precisely put electrons where we want the metal to grow.”
Compared with other metal-healing techniques, the redox process requires much less energy. “We’ve shown we’re six orders of magnitude more efficient,” Pikul says. “Because electrolytes are liquid and mobile at room temperature, you can do this at room temperature, or colder.” The researchers have shown that the technique can return metals to full strength, or greater, in a matter of hours.
Put it together
Despite more and more of the technologies required to construct self-healing robots being developed, they sit mostly in isolation. For sophisticated self-healing robots to emerge, researchers now need to characterize and benchmark these materials, Vanderborght says, so that commercial interests can compare them and match them to specific applications. “It’s a matter of having a portfolio of products: autonomous, non-autonomous, stiff, non-stiff, conductive, magnetic,” Vanderborght says. “We can shop from the different materials and combine them in one big application.”
One of the factors most likely to drive the adoption of these materials is sustainability. Last year, for example, the European Parliament backed draft legislation that would obligate manufacturers to produce goods that are durable — and repairable. Robots with the ability to heal will operate for longer than will ones that can’t, and should therefore contribute less to electronic waste. “Self-repair has a lot of implications for reducing that,” Tee says. “That’s what drives me.” Vanderborght’s group is also aiming to make components that can be mechanically or chemically recycled when they do eventually reach the end of their life.
If the aim is to extend a robot’s useful life, however, then the ability to heal will ultimately be only part of the solution — ideally, a robot would be able to prevent serious injury in the first place. “In the extreme case, you can anticipate damage and avoid it completely,” says Tee. Some hints of this can already be seen in the soft quadruped robot that Shepherd’s team developed. The robot’s fibre-optic sensors measure at sufficiently high sampling rates that a response to any contact could be quickly issued. “Reflexes are going to be really important,” Shepherd says. “It’s not self-healing, but it is damage intelligence.”